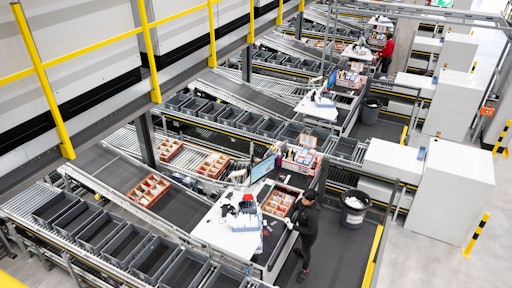
When asked about implementing warehouse automation solutions, many supply chain companies respond with, “I don’t have time, I don’t know what I’m doing, I don’t know where to start, I don’t have the money.”
But all too often, it’s those same companies who also don’t fully understand the implementation journey and what it takes to actually break down the supply chain and parts of the warehouse to better realize the whos, whats, wheres, whens and whys.
That’s why it’s best to start by identifying the “biggest pain points—whether it's labor shortages, inefficiencies, or compliance risks—and focus on quick-win automation solutions that deliver immediate value,” says Steve Pullo, EVP, Made4net. “Begin with foundational systems like a warehouse management system (WMS) for inventory visibility and tracking, then layer in technologies like barcode scanning, temperature monitoring, or robotics as your needs evolve. The key is to start small, scale strategically, and ensure each investment aligns with your long-term operational goals.”
For companies looking to start the automation journey, the first steps will depend on the types of problems they’re looking to solve, their automation budget and where they want their business to be in 5-10 years, according to Josh Hartman, market development director, Dematic.
“Some entry-level automation solutions are smaller investments, such as automated guided vehicles (AGVs) and autonomous mobile robots (AMRs), robotic palletizers and de-palletizers, layer pick solutions, voice-picking solutions, and more. The usage of AGVs and AMRs to convey pallet-sized loads throughout the warehouse is a relatively low-risk entry into automation while still significantly lowering labor costs,” says Hartman. “Another good entry point into automation is integrating existing operations with software. For example, a robust WMS manages inventory, a warehouse execution system (WES) will manage the flow and assignment of work, and a control tower will monitor and alert you to changes in product trends or performance. However, while these are great solutions for specific needs, it’s critical to understand not only where your business is and what it needs today, but [also] what it will likely need in the future to maximize the return on investment.”
Starting with a WMS is also ideal for cold chain organizations “because it serves as the backbone for efficient, accurate, and streamlined operations,” says Keith Moore, CEO, AutoScheduler.AI. “A robust WMS enables real-time inventory tracking, improves order accuracy, and ensures compliance with temperature-sensitive storage and handling requirements. By integrating advanced automation technologies such as automated guided vehicles, robotics, and IoT sensors, a WMS can provide the data and insights needed to optimize workflows and reduce operational costs.”
“Companies are trying to build AI into their operations to streamline decision-making. To start the AI journey, organizations need to make sure the data is good. Then, they need to build a data process map to uncover gaps in the data,” he adds.
For companies beginning their automation journey, it’s important to evaluate the facilities vs. the staffing needs to better understand where automation solutions can help improve efficiency, save on costs, and reduce downtime, says Merry Frain, product manager, industrial inspections, Boston Dynamics.
“Because many companies are facing staffing shortages and don’t have enough hours in the day to complete the tasks needed to keep facilities running efficiently, automation can create efficiencies of scale. Whether it’s industrial inspections or unloading trucks/shipping containers, automation can make a major difference,” Frain says.
“For example, at the Anheuser-Busch InBev (AB InBev) brewery in Leuven, Belgium, Spot conducts 1,800 individual inspections each week across 10 packaging lines that churn out over 50,000 containers of Stella Artois, Budweiser, and Corona beer every hour. In its first six months of deployment, Spot discovered nearly 150 anomalies and slashed average repair times from a few months to 13 days. This is merely one example of success, but evaluating where automation solutions can save companies time and money is the first place to start,” Frain adds.
Exotec
It's also best to evaluate the pain points.
“Are you having trouble sequencing your orders to make sure the pallets are properly stacked? Do you need a better process for packaging your products? How can we efficiently increase order fulfillment without sacrificing precision? Once you identify your key goals, then you can start looking into the solution that can fill these gaps within your warehouse,” says Andy Williams, EVP, Sales North America, Exotec. “Make sure your strategy is based on a solid evaluation of the supply chain level goals and that your data/process that creates the business case for automation in a warehouse is well understood. From there, set clear goals for the automation project and what would determine ROI. This allows the providers you are discussing with truly understand what you need, so they can ensure they’re setting you up with the right system to meet your needs.”
Subscribe to our bi-weekly e-newsletter: Cold Chain Insights
For other companies, it’s best to map out a strategic, phased approach.
“Begin by thoroughly assessing current operations to identify pain points and multiple touch points within current workflows. Prioritize ‘quick win’ technologies like a warehouse management system that includes an order management system (OSM) and inventory automation, barcode/RFID scanning, and report automation for immediate ROI. Gradually scale up to more advanced solutions like autonomous mobile robots, automated sorting systems, and AI-driven analytics. Crucially, prioritize cybersecurity and data protection throughout the process,” says Andrew Wallen, director of distribution, ITF Group. “Finally, invest in training and upskilling training and SOPs for your workforce to adapt to the new technologies and focus on higher-value tasks. This phased approach, starting small and scaling strategically, will improve efficiency, security, and position companies for long-term success.”
It’s also important for companies to understand that deploying automation technology is a journey, “and depending on the types of automated solutions being implemented, typically takes 2-3 years from the start of the journey to when the site is fully operational and ramped up to full volumes,” says Tim Mosier, sales director, integrated solutions, Swisslog Americas. “To begin that journey, you need to first identify what you want to accomplish with the deployment, focusing on operational challenges you are trying to overcome, objectives you want to achieve. And then do your research and assess your options so you can adequately determine the right technology to deploy and the right approach to take. Visit sites where automation technology has been deployed. Speak with the users of automation technology about how their business has changed with the deployment.”
“Depending on the types of automation, most solutions are designed to operate for more than 30 years. It is critical to partner with an automation provider that not only has the right knowledge, people, technologies, software, and capabilities at the start of the automation journey, as well as the history and structure to support your organization and the automation for the duration of the automation life cycle,” he adds. “It is also important that your team is involved throughout the journey to not only gather feedback and ideas, but also to have ownership of the solution and its success. Share the success story and build the enthusiasm along the automation process with your teams at the appropriate stages. This happens at all levels of an organization and is a key factor to a successful automated warehouse.”