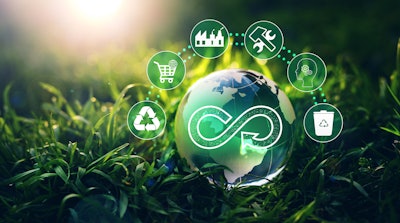
A circular supply chain consists of products and its parts being returned or processed so they can be repaired, resold, refurbished or recycled. It involves minimizing waste, maximizing resources and obtaining resiliency, safety and sustainability. It also comes in many forms, impacting the cold chain in various ways.
While some progress has been made in integrating sustainability, many companies have an opportunity to better reap the benefits by further developing such programs, according to new research from The Conference Board.
That’s because moving goods and ingredients within the supply chain efficiently and quickly is critical to today’s food manufacturers, according to Alex Hempel, senior director of retail supply chain VST, ORBIS Corporation.
“The circular economy concept — which is based on a continuous flow of product in the value circle — is the future of a successful, sustainable supply chain. It focuses on the 3Rs, designing out waste (reduce), keeping products in use (reuse) and regenerating natural resources (recycle/repurpose),” adds Hempel.
Case in point: obtaining and nurturing a circular cold chain is imperative to the future of food logistics.
To boot, nearly three out of four companies surveyed by Aras say they feel pressured by customers, investors, and even their own workforce to operate more sustainably.
Here’s a breakdown of the different ways the cold food chain can move product from Point A to Point B in the most sustainable way possible.
Planning for zero-emissions
One way to reach a circular supply chain is to plan for and implement a zero-emissions trucking fleet.
The Department of Energy and the Department of Transportation released a detailed charging infrastructure plan to support the wide-scale adoption of zero-emission heavy-duty vehicles across the United States. The plan includes four phases of implementation between 2024-2040 and will guide federal and state government and private-sector investments to develop charging infrastructure.
“Electric trucks are the future of the trucking industry,” says Jason Mathers, AVP for Environmental Defense Fund (EDF)’s zero-emission trucks initiative. “Hundreds of fleets are operating these trucks today or have them on order. This plan prioritizes investments in charging infrastructure to match this path of growth. Today’s announcement meets this moment with a long-term plan that should give fleets the confidence to scale their electrification efforts and state policymakers a roadmap to support the zero-emission transition.”
Full electrification of a U.S. commercial truck fleet would require nearly $1 trillion in infrastructure investment alone.scharfsinn86 AdobeStock_460441554
This announcement comes on the heels of a $3 billion commitment from the Environmental Protection Agency (EPA) to fund the transition to zero-emission freight trucks, marine vessels and port handling equipment and the infrastructure to fuel them at U.S. ports.
Two new analyses from EDF show strong growth in both electric vehicle (EV) sales and manufacturing investments in the United States.
In the last three years, the United States has had more private investments in EV manufacturing than any other region of the world. Since 2021, the industry has seen substantial changes to U.S. policies supporting EV manufacturing and jobs, including both production and consumer tax credits under 2022’s Inflation Reduction Act.
“Despite some recent suggestions to the contrary, actual data show the U.S. markets for electric vehicles are flourishing. Sales are better than experts had very recently expected they would be, and the U.S. is now leading the world race for new EV manufacturing investments,” says Ellen Robo, manager of transportation and clean air policy at EDF.
Yet, with more than half of fleets (65%) feeling environmental pressure to transition to alternative energy, many are operating a multi-energy fleet or are about to begin their transition while still experiencing a lack of awareness and trustworthy guidance, according to survey results from Teletrac Navman. In fact, Two-thirds of global fleets are currently operating PHEV, BEV or FCEV vehicles in their fleet.
“Fleets of all sizes and scales are already planning and navigating their transition, but we know there simply isn’t enough credible information out there to help simplify what is a complex move for any business. Alternative energy is still such a new concept for many fleet operators and the process of switching can feel overwhelming,” says Alain Samaha, global president and CEO of Teletrac Navman.
Gasoline, diesel, natural gas and propane continue to be the primary fuel and technology choices for U.S. commercial trucks, with the population of advanced technology near-zero emissions diesels increasing 4% over 2022, according to the Engine Technology Forum (ETF).
“As more of the nation’s trucking fleet adopts the latest generation of advanced diesel and natural gas technology, communities are experiencing cleaner air and lower greenhouse gas emissions. And truckers save on their fuel expenses, too. Previous research showed the significant climate, fuel savings, and clean air impacts in the U.S. of the newer generation (2010 and later model year) of advanced diesel in Class 3-8 heavy-duty trucks. From 2010 through 2030, this generation of diesels will save approximately 1.3 billion tons of carbon dioxide emissions, 130 billion gallons of fuel, yield a cumulative savings of 1 million tons of particulate matter and 18 million tons of nitrogen oxide emissions. These benefits will be even greater once new emission regulations are implemented for new vehicles starting in 2027,” says Allen Schaeffer, executive director of ETF.
However, an emerging trend in converting food residues into biodegradable disposable items or part of the product has grown in the last five years.
Based on representative network loads and routes from Ryder’s dedicated fleet operations in today’s market and other factors, data shows the annual total cost to transport (TCT) by EV vs. diesel is estimated to increase across the board – ranging from up to 5% for a light-duty transit van to as much as 114% for a heavy-duty tractor (depending on the geographic area). And, for a mixed fleet of 25 light-, medium- and heavy duty vehicles, the analysis shows an increased TCT of up to 67% for an all-electric fleet.
“While Ryder is actively deploying EVs and charging infrastructure where it makes sense for customers today, we are not seeing significant adoption of this technology,” says Robert Sanchez, chairman and CEO of Ryder. “For many of our customers, the business case for converting to EV technology just isn’t there yet, given the limitations of the technology and lack of sufficient charging infrastructure. With regulations continuing to evolve, we wanted to better understand the potential impacts to businesses and consumers if companies were required to transition to EV in today’s market.”
However, fleets list unstable fuel costs, equipment/vehicle maintenance and purchasing new equipment/vehicles as their Top 3 expenses, according to the Teletrac Navman study.
That’s because transitioning to zero-emissions comes with a price tag.
A report from American Transportation Research Institute (ATRI) concludes that relying on battery electric vehicle (BEV) to decrease CO2 emissions is nearly six times more expensive than using renewable diesel (RD).
Overall, ATRI estimated that a transition to BEV for long-haul trucking will cost over $1 trillion in electric infrastructure and vehicle purchase costs over 15 years. However, to achieve similar CO2 benefits with RD, ATRI estimates a price tag of $203 billion, a significant cost savings for achieving the same environmental benefits. Since RD is considerably more scalable than BEV and can be deployed immediately in trucks without modifications, it is likely that CO2 benefits using RD can be achieved on a much shorter timeline than with a BEV transition.
In fact, full electrification of the U.S. commercial truck fleet would require nearly $1 trillion in infrastructure investment alone, according to a new report released by the Clean Freight Coalition (CFC).
The study forecasts a realistic infrastructure buildout for the electrification of medium- and heavy-duty commercial vehicles, exposing what the CFC calls a massive investment gap as state and federal policymakers mandate increased adoption rates of battery-electric commercial vehicles. Preparing today’s commercial vehicle fleet for electrification would require the commercial vehicle industry to invest upwards of $620 billion in charging infrastructure alone, including chargers, site infrastructure and electric service upgrades. And, utilities would need to invest $370 billion to upgrade their grid networks to meet the demands of just commercial vehicles.
This nearly $1 trillion expenditure does not account for the cost of new battery-electric trucks, which according to market research can be 2-3 times more expensive than their diesel-powered equivalents, according to CFC. For example, a diesel Class 8 truck costs roughly $180,000, while a comparable battery-electric truck costs over $400,000. While medium-duty vehicles will face fewer roadblocks, economic and operational constraints make electrification very challenging for the heavy-duty segment.
“Electrification means focusing on the vehicle segments that are easier first; it means that we have to look at how fleets operate and potentially adjust; it means that we need better cooperation and planning across industries and governments; and it requires an openness to alternative technology paths to decarbonizing the heavy-duty segment,” says Roland Berger, senior partner, Dr. Wilfried Aulbur, and author of the report. “It also is clear that an industry with a yearly turnover of about $800 billion and a profit margin around 5% cannot invest $620 billion without financial support or a significant increase in freight rates.”
Packaging for the future
Supply chain packaging that doesn’t flow efficiently within a supply chain and can’t be consistently filled, stored, shipped, used or returned for replenishment and reused in a continuous cycle is a major challenge to building a circular food chain, says Hempel. Annual packaging costs, transportation inefficiencies and packaging that is not specially designed to nest or collapse when empty continue to pose challenges. CLICK HERE to read the exclusive interview with Alex Hempel.
In response, ORBIS launched the reusable Odyssey Pallet, which travels more than 400 trips in the supply chain, compared to 11 trips for a wood pallet, helping reduce waste associated with single-use pallets, decreasing automated system downtime related to inconsistent packaging and improving plant cleanliness.
ORBIS Corporation released the Odyssey 3-runner pallet to enhance dimensional consistency, transportation and hygienic.ORBIS Corp.
ORBIS also launched packaging life-cycle assessments (PLCAs), designed to help companies calculate the impact reusable packaging can have on the environment.
“Using life-cycle assessments to compare reusable and single-use packaging, ORBIS applies data-driven analysis to help customers reduce their overall environmental impact in terms of greenhouse gas (GHG) emissions, water, solid waste and energy usage. This unbiased analysis provides companies with measurable data as they make the switch to reusables,” says Hempel.
ORBIS also launched a series of totes designed for use in automated systems, complete with automation locators to ensure proper tote placement and hybrid bottoms.
Another emerging trend entails converting food residues into biodegradable disposable items.
The use of pineapple peels, corn, avocado pits, and other materials, for instance, grows in the United States and Latin America to reduce pollution. Meanwhile, alternative materials such as bamboo, sugarcane, or cassava, which are biodegradable and natural, are used to package food.
“Despite a growing trend to improve the food supply chains from farm to fork and back to farm, scalability is the biggest challenge,” says Christopher Mejia-Argueta, research scientist and director of the Food and Retail Operations Lab, MIT Center for Transportation and Logistics. “Supply chain coordination requires diverse stakeholders to align efforts from farmers to consumers and from consumers upstream to recover edible food. However, this coordination is challenging because it requires collaboration, synchronization, and stakeholder trust.” CLICK HERE to read the exclusive interview with Christopher Mejia-Argueta.
Protecting the food chain
There are a few key drivers to creating a circular food chain. One major one being how to make participation in a circular economy economically viable, says John Reich, scientific program director, Foundation for Food & Agriculture Research (FFAR).
“Some solutions would require longer-term investments to get there and understanding how any solutions can integrate into existing structures and supply chains is also important. Creating solutions that are efficient and sustainable is also important,” says Reich. CLICK HERE to read the exclusive interview with Reich.
FFAR is awarding $954,556 to Colorado State University (CSU). CSU, Cornell University, Glynwood Center for Regional Food and Farming, NY Farm Viability Institute and The Rockefeller Foundation to better understand and investigate food procurement.
Organizations must start by understanding the primary purpose of starting a sustainable journey, what they want to get, and how they want to measure it.songwut AdobeStock_832231727
Last year, in partnership with the Biosciences team at Schmidt Sciences, FFAR hosted the Feedstocks of the Future Convening, bringing together leading experts in the field to identify challenges and opportunities for a circular U.S. bioeconomy. One of the major challenges identified was determining feasible and economically viable uses for agricultural and food industry feedstocks.
“Obtaining homogeneous feedstocks that have sufficient quantity to be a feedstock and collecting and processing the feedstocks are some (but not the only) of the challenges,” adds Reich. “Some of this relates to the supply chain for these feedstocks, as this would need to be developed. Developing new potential products with new potential feedstocks is a first step— scientific solutions must also be scalable.”
For its part, the Food Systems Countdown Initiative (FSCI) identified a framework composed of 50 indicators that monitor agriculture and food systems at a global level, using existing data to enable immediate action. Repurposing existing data, rather than carrying out new research means policymakers have quick access to relevant information.
“You can’t manage what you don’t measure. That’s why we need a monitoring system that shows strengths and weaknesses at national, regional and global levels across all parts of agriculture and food systems. And this complete picture highlights successes that provide valuable lessons for others,” says Mario Herrero, professor and director of the food systems and global change program, Cornell University.
Starting a sustainability journey is not trivial. Any organization must start by understanding the primary purpose of starting this journey, what they want to get, and how they want to measure it, Mejia-Argueta says.
“After defining this initial vision, organizations must conduct a baseline assessment to identify gaps, set clear SMART goals, and prioritize their efforts. Also, organizations should educate leadership and staff about the significance of sustainability, create a change management plan, and engage stakeholders to gauge their expectations. Immediately after, organizations must start analyzing their current practices and find ways to improve them based on their new sustainable vision,” he says. “There is no consensus on creating adequate incentives for businesses to adopt circular practices without requesting them to invest time and money. In addition, mandatory regulations on circular economy have grown for specific resources, such as water and food waste from restaurants, but not across industries. Moreover, their application has been limited to geographies focused on reducing carbon footprint, improving resource use, and mitigating adverse impacts on local ecosystems. However, overcoming these challenges requires a multi-faceted approach involving technological innovation, policy support, stakeholder collaboration, and widespread consumer engagement.”
Obtaining and nurturing a circular cold chain is imperative to the future of food logistics. From zero-emissions fleet to sustainable packaging to protecting the overall food chain, there are many ways companies can move product from Point A to Point B in a sustainable fashion. For many, it’s about identifying the gaps, developing a plan and executing that plan. And, every little bit helps.