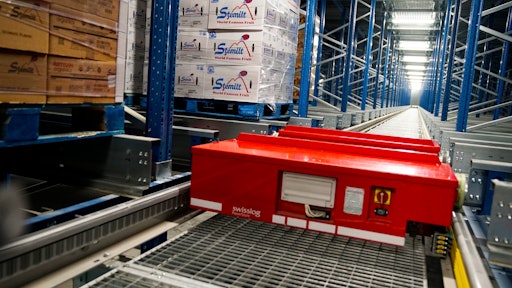
2024 is projected to be the year for major adoption and implementation of warehouse automation.
Thankfully, these true problem-solving solutions are prepping cold food chains for anything and everything.
Food Logistics talks exclusively with Sean Wallingford, president and CEO of Swisslog Americas, about why the business case for warehouse automation has never been stronger and the return on investment has never been shorter.
CLICK HERE to read the article in full.
Food Logistics: Warehouse automation continues to be on the rise. What do think is attributing to the growth in adoption of automated warehousing?
Sean Wallingford: As companies continue to deal with labor shortages, although not to the extent of the last few years, warehouse automation solutions are providing a means for them to maintain productivity and efficiency levels while dealing with a reduced labor force. A number of companies are also using automation technology as a way to attract potential employees or retain existing ones.
As the technology and ease-of-use continues to advance, many companies are seeing automation systems as a viable business option that lower operational costs. For instance, we recently introduced the next generation of our CarryPick mobile robotic goods-to-person storage and retrieval system, which offers high scalability with low operational costs. It features faster, more agile automated guided vehicles (AGVs) to increase performance levels and shorten the return on investment for customers. The system’s scalability enables companies to accommodate growth without adding additional labor.
Food Logistics: What kinds of automated solutions/technologies has your company introduced within the last 12 months? Anything on the horizon that will be introduced soon?
Wallingford: As more businesses adopt automatic mixed-case picking and palletizing in answer to SKU proliferation, pallet automation that enables mixed-case palletizing is becoming more important. For instance, Swisslog has developed ACPaQ, a robotic and data-driven case picking and palletizing solution for store-ready order fulfilment. The highly flexible solution takes single SKU inbound stock pallets, breaks them down to cases and builds them back up into mixed SKU outbound order pallets. Our solution is scalable for mid-size, and large distribution centers and Swisslog’s SynQ palletizing software allows companies to customize the palletizing order to increase efficiency during in-store replenishment.
We also recently introduced the latest evolution of our robot-based item picking system, ItemPiQ. It features significant improvements made possible by advanced AI capabilities, such as context-aware picking and improved item recognition. ItemPiQ is designed for repeated, reliable picking of a wide range of items to fulfill fast delivery of orders at low operating costs, streamlining and improving the order picking process. Every aspect of the system is handled within the Swisslog family of companies, from the vision camera to the robot and the software. For reliable and effective operation in a complete Swisslog system, the robot cell can be fully integrated into the SynQ warehouse management system.
We are also working closely with customers to deploy the latest AutoStore R5 Pro Robot. This new robot is designed to address the specific demands of large-scale e-commerce operations, emphasizing better space usage, higher performance, and reduced total ownership costs for companies running multishift operations at scale.
Food Logistics: What advice do you have for those companies who haven’t implemented any automation whatsoever or are just starting the journey? Where/how should they start?
Wallingford: The business case for warehouse automation has never been stronger, and the return on investment has never been shorter. Nevertheless, organizations both large and small face a significant hurdle in securing the required capital, when advancing automation initiatives.
The good news is that financial options are available today for moving ahead with warehouse automation. Previous systems would sometimes become obsolete before realizing any ROI. But the promise of performance and the ROI of new-generation systems reduce the risk for financial services companies.
This is enabling financial services providers to offer fiscal solutions that cover the complete solution investment, including soft costs such as software, configuration and installation, and have end-of-lease terms that are well-defined upfront and very favorable to the leasee.
In addition to providing financial options for companies planning to automate, these leases create opportunity for organizations that might have thought automation was beyond their reach. Now, small and medium-size businesses can add the automation needed to keep pace with larger competitors, while third-party logistics providers can align lease terms with their customer contracts to protect themselves from financial exposure at contract end.
Food Logistics: How can companies decipher which automated solutions are best for their warehouses?
Wallingford: There are a number of warehouse automation technologies available today—and more coming in the future—and this can be overwhelming for organizations considering automation. But it also allows the technology to be precisely matched to the application.
To identify the appropriate automation, it is important to work with vendors that support a broad range of warehouse technologies and take a technology-agnostic approach to each deployment. That means beginning each engagement with the data and letting the data dictate system selection. Plus, with the inherent flexibility of today’s automation systems, picking the wrong technology is harder than ever.
Additionally, we have reached the point where we do have automation best practices, much of which focus on the design and configuration of the system, as well as on the implementation and the operational side. Most of these best practices come from early automation adopters and can help guide other companies as they determine their automation strategy and deploy automation solutions.
Food Logistics: In your opinion, which are the best types of automated solutions and why? Think AI, cloud-based, IoT, connectivity and more.
Wallingford: Artificial intelligence (AI) is making the warehouse of the future more dynamic, more agile, and more responsive. The intelligent networking of machine, process and product information is a quantum leap for process optimization. For instance, AI enables robotics to self-learn from experience, which means that robotic picking ability improves over time with enhanced picking strategies for new products.
Take the Swisslog ItemPiQ as an example. This articulated arm robot is designed for repeated, reliable picking of a wide range of items to fulfill fast delivery of orders at low operating costs. The identification of items and their optimum grasping point for successful picking is optimized by applied AI over time. It uses an intelligent 3D vision system to identify individual objects in the source bin. In combination with the software algorithm, the system determines grasping points of new products, which allows the robot to continuously learn, eliminating the need for a time-consuming teaching process for items.
Food Logistics: What are some things not addressed above that may be pertinent to our cold food chain readers?
Wallingford: One of the advancements we see on the horizon for robotics is the growth of connected and intelligent systems. As solutions become more standardized, it becomes easier to leverage data (e.g., edge data, sensor data, product data, operational data) to make more insightful and effective operational decisions. This standardization is especially important for AI-enabled solutions. Maturity in solution design and software platforms will enable companies to leverage these technologies and the information that are more widely in use outside of our industry.
In regard to those software platforms, we expect further productization of software platforms from integrators like Swisslog. This will bring a level of standardization to software that will be more beneficial than customized software, especially in the long term. This will include increased flexibility and configurability, as well as a framework for continued evolution of robotic systems. The risks that come with the larger, more complex integrated systems require more collaboration with customers on reducing risk through more standardized, productized solutions.
CLICK HERE to read the article in full.