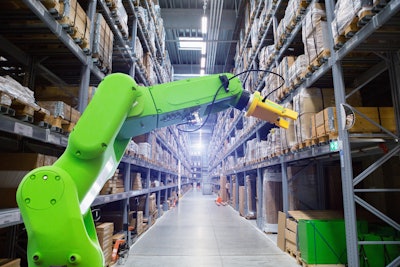
In today's fast-paced world, the warehousing and logistics sector plays an essential role in ensuring that products move smoothly from suppliers to end consumers. With the growing demand for faster, more accurate deliveries, businesses are increasingly turning to advanced technologies, and one such game-changer is warehouse robotics.
These automated systems are revolutionizing the way warehouses operate, driving efficiency, improving accuracy, reducing labor costs, and enhancing the overall customer experience.
The emergence of warehouse robotics
Over the past few decades, the warehouse and logistics industry has witnessed remarkable advancements in automation. What once relied solely on human workers to perform labor-intensive tasks is now being transformed by robots designed to enhance speed, accuracy, and cost-effectiveness. Warehouse robotics involves the deployment of various robotic systems that handle key functions such as picking, sorting, transporting, and storing goods.
While traditional warehouse operations are often associated with manual labor and large-scale operations requiring human involvement in repetitive tasks, robotics in warehouses offers a substantial leap in productivity. With the growing e-commerce industry, there is a greater need for dynamic and rapid inventory management solutions, and robots are addressing this demand by performing tasks such as fetching items, sorting orders, and stacking materials, while cutting down the risk of human error.
Benefits of warehouse robotics
- Increased operational efficiency. Robots in warehouses automate time-consuming tasks, such as product picking and packing, ensuring faster processing of goods. This improved workflow increases overall operational efficiency, enabling warehouses to handle a higher volume of goods and meet deadlines.
- Reduced labor costs. With robots performing monotonous and physically demanding tasks, businesses can reduce their dependence on human labor for tasks like moving heavy objects, retrieving items from high shelves, and handling bulky packages. This not only cuts labor costs but also mitigates risks related to workplace injuries.
- Enhanced accuracy and reduced errors. Unlike humans, robots are programmed to work with precision, eliminating the chances of human errors in tasks such as stock-taking or picking incorrect products. This accuracy helps maintain inventory levels in real time and ensures customers receive the right products in their orders.
- Better safety standards. Automating hazardous tasks reduces the risk of workers injuring themselves, especially in environments with heavy equipment, sharp tools, or hazardous materials. By deploying robots for such operations, workplaces become much safer.
- Scalability and flexibility. Robots are highly scalable, offering solutions for different warehouse environments and workloads. Systems like automated guided vehicles (AGVs) or autonomous mobile robots (AMRs) can scale up or down depending on a company’s operational needs, offering more flexibility in demand fluctuations.
- Faster ROI. While initial investment in warehouse robotics can be high, the long-term benefits of efficiency, reduced labor costs, and improved accuracy generally lead to quicker returns on investment.
Types of warehouse robotics systems
Several types of warehouse robotic systems exist today, with each designed for specific warehouse functions:
- AGVs are mobile robots equipped with cameras and sensors to navigate the warehouse without human intervention. These vehicles can be used for transporting materials from one location to another, improving the flow of products throughout the warehouse.
- AMRs are more advanced than AGVs as they use artificial intelligence (AI) to determine their paths within the warehouse. AMRs can interact with other robots and perform a wide range of tasks, such as transporting inventory, monitoring warehouse environments, and even assisting in stock management.
- Robotic arms are used for tasks like picking products from bins, packaging, sorting, or assembling products. These robots use machine learning and AI to perform tasks with a high degree of dexterity and precision, even in confined spaces.
- Robotic shelving systems retrieve products from various storage units or move items to the storage zone. These systems are designed to optimize shelf space by keeping items in narrow, stacked environments.
- Drones are increasingly used in inventory management within large warehouses. They are capable of scanning barcodes, checking the stock levels on shelves, and performing high-level inspections of large warehouse spaces from above.
Challenges in implementing warehouse robotics
While warehouse robotics presents a myriad of benefits, its implementation comes with certain challenges that businesses must carefully consider:
- High initial investment. The cost of deploying robots is one of the most significant barriers to entry, particularly for small to medium-sized companies. The cost includes robot purchase, installation, maintenance, and staff training, all of which may take years to recoup.
- Integration with existing systems. Implementing robots in warehouses involves integrating them with existing supply chain management, enterprise resource planning (ERP), and warehouse management systems (WMS). This integration can be complex and time-consuming, requiring adjustments to existing workflows.
- Maintenance and technical issues. Robots require regular maintenance to ensure they operate smoothly. Technical failures, glitches in AI programming, or sensor malfunctions can disrupt warehouse operations and cause costly downtime.
- Workforce resistance. Automation can lead to concerns over job displacement. Warehouse employees may fear the loss of jobs due to increased automation, although the need for human oversight, maintenance, and management of the robots still creates ample job opportunities.
- Cybersecurity risk. With increasing digitization, the safety of automation systems becomes paramount. Robotics rely on wireless communication and cloud-based data storage, which can make them vulnerable to cyber threats if not properly protected.
Future of warehouse robotics
Looking ahead, the use of robots in warehouses is expected to become even more widespread. Trends indicate the following developments in warehouse robotics:
- AI and machine learning. With advancements in AI, robots will continue to improve their decision-making capabilities, allowing for real-time adjustments based on warehouse conditions. AI-powered robots will become more intuitive and able to deal with complex tasks autonomously.
- Collaboration between humans and robots. In the future, warehouse robotics will increasingly focus on collaboration between human workers and robots. Known as collaborative robots (cobots), these systems are designed to assist workers with physical tasks and share duties in a way that maximizes productivity.
- Integration with supply chain management. Robotic systems are expected to become more integrated with end-to-end supply chain solutions, sharing data seamlessly across various platforms and systems, leading to greater overall efficiency.